Le risque mécanique
Les nombreuses machines misent sur le marché doivent être conçues et construites de façon à ce que leur mise en place, leur utilisation, leur réglage, leur maintenance, dans des conditions conformes à leur destination, n’exposent pas les salariés à un risque d’atteinte à leur santé et sécurité.
Définition :
Une machine est un ensemble de pièces ou d'organes liés entre eux dont au moins un est mobile et le cas échéant, d'actionneurs, de circuits de commande et de puissance réunis de façon solidaire en vue de transformer, traiter ou conditionner des matériaux ou déplacer des charges.
- Un ensemble de machines qui concourent à un même résultat et sont solidaires dans leur fonctionnement est considéré comme une machine.
- Un équipement interchangeable destiné à être assemblé à une ou plusieurs machines différentes par l'utilisateur lui-même en vue d'en modifier la fonction est considéré comme une une machine.
Le risque mécanique est le risque lié à une défaillance humaine ou technique à l'occasion de l'utilisation d'une machine fixe ou mobile ou d'un équipement de travail.
Les machines et équipements de travail constituent des sources de danger potentiel pour les opérateurs en raison :
- Des risques liés au type d'énergie utilisée (électricité, gaz, charbon, vapeur.)
- De l'existence de partie en mouvement accessibles par l'opérateur : (organise de transmission, pièces, outils, ...)
- De l'existence de matières ou de fluides pouvant être rejetés sous pression (pièces, copeaux.)
- De l'utilisation d'outils tranchants
- De la non consignation de la machine lors de sa réparation ou de sa maintenance
- De l'existence de parties brulantes accessibles
- Du niveau sonore de son fonctionnement anormalement élevé
- De l'utilisation ou de l'émission de polluants au cours de son fonctionnement
- Des postures contraignantes pour l'opérateur pour exercer son activité (contraintes posturales, gestes répétitifs, vibrations ...)
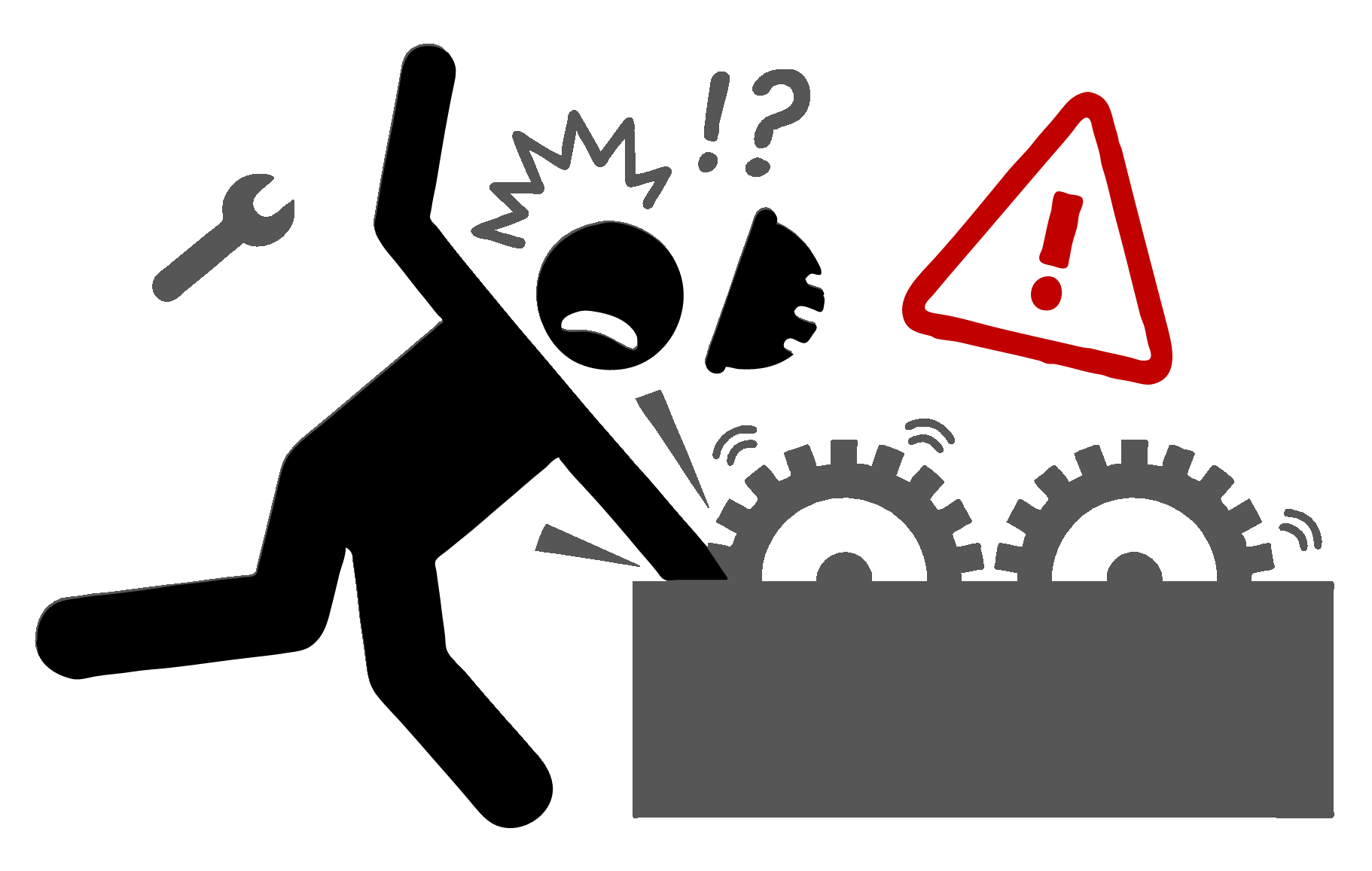
Le risque mécanique peut prendre plusieurs formes :
- Un dysfonctionnement mécanique d'une machine ou d'un véhicule peut être responsable sur du matériel ou des personnes de :
- Coincement (d'une pièce, d'un doigt, d'un membre...)
- Pincement
- Entraînement (d'une pièce, d'un vêtement, d'une chevelure...)
- Cisaillement
- Ecrasement
- Projection : de liquide, de vapeur, de poussières, de pièces détachées, de la pièce en cours d'usinage, de copeaux...
- Choc (par un véhicule ou sa charge)
- Une défaillance du système d'aération et d'assainissement peut provoquer des intoxications plus ou moins graves.
Le risque est d'autant plus élevé que :
- L'équipement est nouveau, en cours d'essai
- Il est mal réglé
- Le personnel est peu formé
- La pression de temps conduit à des prises de risque (décapotage, oublie des procédures de confinement, vitesse...)
Les risques peuvent être de gravité très variable.
Accidents par contact direct avec un organe en mouvement :
- Ecorchures, égratignures
- Ecrasements
- Coupures
- Sectionnement
- Arrachement
- Fracture
- Electrisation
Accidents par projection :
- Brûlures
- Contusions
- Inclusion de corps étranger (huiles...)
Principes généraux de gestion du risque mécanique
L’appréciation du risque
1. Délimiter les limites de la machine
2. Repérage des phénomènes dangereux
3. Estimation du risque
La réduction du risque
4. Elimination des phénomènes dangereux
5. Utilisation des protecteurs et dispositifs de protection
6. Avertissements, méthodes de travail
7. Formation et information
Il est indispensable aujourd’hui, malgré un ensemble de mesures tenant à la fois à la prévention matérielle (EPI, EPC, aménagement de poste de travail) ou à la prévention organisationnelle (procédures de travail, consignes de sécurité), qui pourrait laisser croire à une liberté sans limite, que le risque zéro n’éxiste pas dans le monde du travail.
La prévention doit donc se faire une place majeure !
Sur le site www.jemconsulting.fr vous trouverez des Quizs, des Jeux et des informations très utiles sur la prévention des risques professionnels (bruit, TMS, stress, produits chimiques, équipements de travail, formations, nouvelles réglementations ....).