La méthode des 5S
Qu’appelle-t-on la méthode 5S ?
C’est une technique de « management japonaise » visant à l'amélioration continue des tâches effectuées dans les entreprises.
La méthode 5S est basée sur l’aménagement du poste de travail et la prise de conscience qu’un environnement propre et rangé est propice à une production de qualité.
L’initiative doit venir du sommet de la hiérarchie, qui doit être impliquée et montrer sa volonté de réussite.
La direction doit formuler, promouvoir un projet auquel tout le monde puisse adhérer et soutenir de façon durable ceux en charge d’exécution.
La méthode 5S permet de réduire, voire d'éviter :
- Le désordre
- La perte de documents
- La détérioration du matériel
- Les accidents du travail
La méthode 5S permet également d'optimiser :
- Le temps de travail
- Les conditions de travail
- Les déplacements
- Indirectement le chiffre d'affaire
Les objectifs de la méthode
C’est une technique simple dont l’objectif est de déployer l’ordre et la rigueur au sein de votre entreprise.
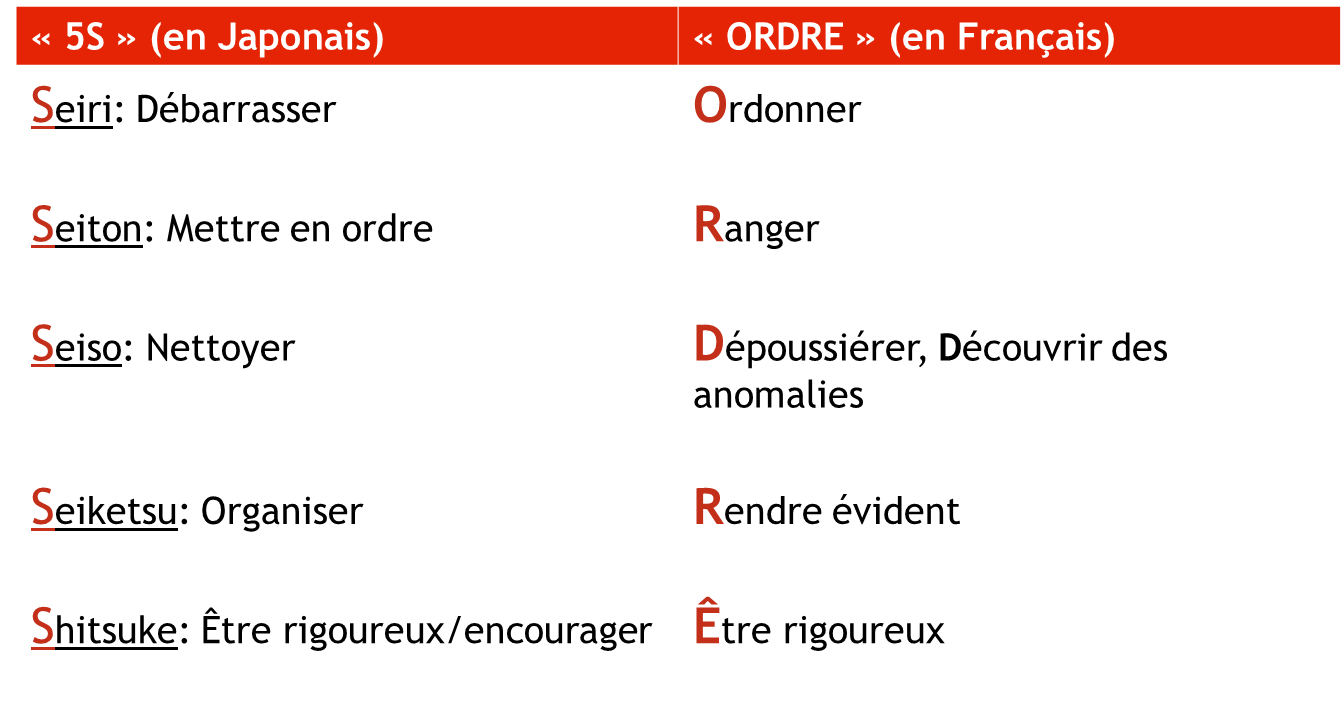
Exemple de mise en œuvre de la « méthode 5S » en 7 phases
Phase 1
La préparation du chantier :
Prendre connaissance de la démarche, utiliser le guide et ses annexes pour préparer tout le matériel nécessaire.
Mettre en place le tableau d'activité et préparer les supports de communication / formation pour le personnel.
Phase 2
Le grand débarras :
Retirer du poste de travail tout ce qui est inutile, à réparer ou à ranger quelque part.
Mise en place de la Z.A.D. (Zone d'Attente de Décision) où seront stockés les matériels faisant l'objet d'un traitement => opération d'étiquetage
Phase 3
La remise à niveau :
Traitement des étiquettes, suppression de la Z.A.D. et mise en place du kit de nettoyage.
Préparation et réalisation de la journée 5S.
Traitement des observations d'anomalies et des idées d'amélioration issues de la journée 5S.
Phase 4
L'affectation :
Définir l'aménagement idéal du poste de travail et réaliser un marquage au sol provisoire avec du scotch de couleur.
Identifier également tous les emplacements: outillage, consommables, documents de travail etc...
Phase 5
Le maintien du standard établi :
Ecrire des gammes de nettoyage, établir un planning journalier, hebdomadaire et mensuel.
Analyser et supprimer les sources de salissures.
Faciliter les accès pour nettoyer, conduire, régler: transparence, rapidité de démontage.
Phase 6
Le pilotage visuel :
Finaliser le marquage au sol à la peinture.
Visualiser les paramètres de conduite, de réglage, de rangement.
Utilise des standards visuels.
Phase 7
La pérennisation :
Mettre en place des audits de maintien pour éviter les dérives.
Réaliser un bilan du chantier et enregistrer les enseignements (+/-).
Finaliser le plan d'actions.
Développer des outils de maintien (gammes de maintenance autonome)
Info :
« A l’origine de cette méthode qui a fait ses preuves et séduit de plus en plus d’industriels : (pour exemple) Toyota, dont l’ambition était de mettre au point une démarche qualitative pour organiser son espace de travail et ainsi optimiser son activité.
Avec pour motivation principale : être plus méthodique pour être plus efficace. »
Sur le site www.jemconsulting.fr vous trouverez des Quizs et des informations très utiles sur la prévention des risques professionnels (bruit, TMS, stress, produits chimiques, équipements de travail, formations, nouvelles réglementations ....).
Jem Consulting développe également une offre globale de conseils et de formations opérationnelles dans les domaines du Management, de la Communication et du RH.